Human Error: What it is and how to mitigate against it
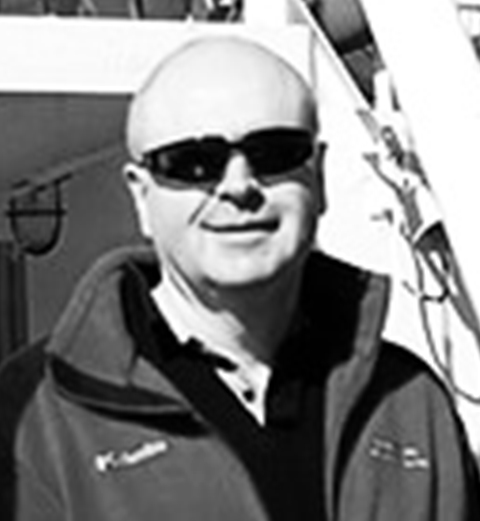
ANDY TILLEARD
EHS Consultant
EazySAFE
It is clear than in terms of accident investigations especially those for major events, these major accidents are never what might be called ‘blue sky’ events. It may seem like that to the people impacted by them but invariably the investigation report will uncover and identify weaknesses and stress in the system that went either unreported or if reported, uncorrected.
The historical trail that is uncovered during an accident investigation becomes quite clear when it is slowly revealed but of course, it is being looked at from a very specific perspective – essentially it is a process of reverse engineering. But a safety management system that has weakness embedded within it will not examined to any degree to identify if there are any early indicators that something is wrong or undesirable events are occurring without correction.
Human Error – Not just an individual’s fault
People in the workplace behave in complex ways and are impacted to varying degrees from both obvious and less obvious influences. In recent years, the term human error has been re-examined in recognition that these influence often put workers into a situation in which a poor decision may be more likely to be made. It’s not that people want to make bad decisions per se but that decision making process happens within an organisational context which can cultivate human error events. The UK Health and Safety Executive published HSG48 – Reducing error and influencing behaviour in 1999 (2nd Ed) which amongst other things, took an overall look at human behavior and its potential impact on health and safety performance. There is a recognition now that when we talk about human error, it is not just saying that a person did something wrong and therefore it was their fault; perhaps this is a subject that employers need to be more acutely aware of, i.e. to what extent has the workplace I have created dictate to some degree the actions of an employee when they need to make decisions and what is my influence when they make the wrong ones?
Human error as defined in HSG48 is broken down into two distinct areas; that of errors and violations. There is not always a direct negative outcome when errors are made but they are undesirable as they present an opportunity for risk controls to be lessened or even short circuited completely. The use of the term violation is deliberate as it implies that an action was intended whereas errors are seen as actions or decisions that were taken but were not intended. Violations are a worry for any organisation as they are a deliberate attempt to deviate from a safe situation into a less safe one, usually in order to save time or money. We shall see later what the real world and financial costs of these violations can be and their potential severity.
What are Errors?
Errors themselves can be broken down into two further subgroups which are mistakes and skill based errors. Mistakes are the most interesting of these error groups simply because people act in a particular way believing that they are doing the right thing even though it’s not the right thing to do. It is almost counter-intuitive to think that such a situation could exist at all but it is common and here’s why. Mistakes are characterised as knowledge or rule based :
-
-
- A knowledge based mistake is what happens when a person is put into a position that he/she does not have the knowledge to manage and we may then rely upon our own experience to attempt to bridge the knowledge gap. For example, consider a safety advisor who has worked in the seismic industry offshore and who is then assigned to a drilling operation. The seismic and drilling industries although related as upstream activities are in reality completely separate. The safety advisor would attempt to use their offshore safety management knowledge which would be common to bridge that industry gap although they would still not be knowledgeable about drilling practices and operations. This knowledge gap may not allow the safety advisor to identify drilling situations which could escalate (e.g. H2S coming onto the drill floor) whereas he would be familiar with hazardous scenarios in his previous position in the seismic industry.
- A rule based mistake occurs when we use familiar and well-known instructions or procedures to undertake a work task but don’t realise that the situation has changed and that the once familiar approach is no longer valid. This type of mistake is often characterised by a lack of communication where workers are not fully or properly informed of changes or existing requirements in the workplace. For example, a forklift driver was not informed about changes to the layout of traffic routes at the facility after a risk assessment identified improvements required to separate workplace vehicles and pedestrians. The driver could have caused an accident by driving to a particular loading area that subsequently had been put off-limits to pedestrians only.
-
Skill based errors are characterised by slips and lapses:
-
-
- A slip is defined as an action that was undertaken but not as planned. They are easy to make because they happen with tasks with which we are very familiar. We all know about renting a hire car and finding to our dismay that the layout of the controls is different to our own car. I’m sure that, like me you have turned the wipers on instead of a turning indicator or flashed a car with full beam headlights instead of putting screen wash onto the windscreen. We have the skill to drive the car but the actions we take are not as intended. In the workplace, this type of situation can develop with tasks such as operating controls on hydraulic system remote control units where the control is pushed up instead of pulled down, where a chemical mixture is made with a 80% mix of chemicals instead of the required 8% or where a number value in imperial units is used in a mathematical calculation for a spacecraft trajectory calculation but it should have been in metric units.
- Lapses occur when we become distracted, miss a step in a work activity or even forget to do something altogether. This is one area where the use of checklists come in very handy for work activities, inspections or checks that need to be systematic and consistent. Have you ever left home thinking did I turn off the cooker, is the over still on or did I lock the front door? At work this can manifest itself missing safety meetings or unscheduled tool box talks, completing an inspection but missing out a particular work area but this type of error can also have severe consequences. In December, 2011 a helicopter crash just outside of Las Vegas killed 4 passengers and the pilot. The investigation found that “The inspector’s fatigue and lack of a work card or checklist clearly laying out the inspection steps to follow contributed to an inadequate post-maintenance inspection.” 2 In effect, the lack of an inspection checklist in this case meant that a degraded self- locking nut and the improper or non-use of a split pin to secure it was not identified by a fatigued inspector and this degraded component went on to be the root cause of a fatal critical flight control failure. By these types of slim margins disasters sometime unfold.
-
What are violations?
Violations should be a considerable worry for any organisation as they are a deliberate attempt to deviate from a process, procedure or work instruction. To an extent, the prevalence of violations is a reflection of the safety culture of an organisation where such behaviors, although they may not be actively encouraged they may be tolerated. There are many types of violations from the minor to the major but organisations also have to be careful that their rules and requirements, such as for the use of PPE is risk and evidence based and no just opinion. We have all been at work locations where there is a particular PPE requirement, such as for safety glasses and you really struggle to understand why they are necessary. Bad law does not make for good behaviors… Violations can escalate in seriousness when acts such as bypassing or removing machinery guards to speed up the work or not undertaking critical maintenance activities due to the cost of spare parts are present. Paradoxically, violations tend to occur with workers trying to do a better, faster or a more efficient job for their employer but the risk / reward ratio is most certainly stacked against the perpetrator. Fortunately, actions on the more extreme end of the spectrum such as willful damage or sabotage are thankfully very rare. Violations come in three subcategories of routine, situational and exceptional.
-
-
- Exceptional violations are hopefully less common but can have significant potential. These events occur where a known rule, safety measure or safety system are bypassed or disabled to expedite an activity, such as removing a machinery guard interlock to speed up a maintenance task on live equipment or not following electrical safety practices because the work can be completed in half the time. The document HSG48 uses the Chernobyl nuclear accident as their own example where they state that “Before the accident at the Chernobyl nuclear power plant a series of tests were being undertaken. When an operator failure led to dangerously low power levels the test should have been abandoned. Operators and engineers continued to improvise in an unfamiliar and increasingly unstable regime to protect the test plan.” 3 That is an incredibly severe outcome for an exceptional violation and although perhaps an extreme example, it is effective in making a point that these types of events can and do happen.
- We are all familiar with routine violations. These happen when deviations to work practices become normalised and accepted, where doing a job in a non-standard way is not penalised or where we think that existing procedures are unnecessarily restrictive and so we work in our own way. The discussion on wearing PPE here is the perfect example of a common routine violation if people don’t understand a requirement or where that is a valid case, the rules are not enforced.
- Situational violations occur in an environment where the situation dictates or influences the work activity. For example, where a work task that has so many steps that it cannot be completed properly in the required time and so the workers routinely deviate from it or where pressure from management push people into delivery timelines which are not realistic, perhaps due to a lack of staff. Remember the deadly Texas City refinery explosion from 2005 which killed 15 people? One observation from the investigation report during the start-up stated “The Superintendent and Training Coordinator stated in interviews that they were unaware that operators were routinely deviating from the written startup procedure…Operators had not informed supervision of these departures from procedures, and there was no system in place to verify that practices conformed to procedures.” 5 In that very specialised and safety critical situation of a process start-up, operators didn’t follow their own procedures. The next question is the ‘why’ question but it is a clear example that these deviations can occur even in major hazard industries.
-
Whilst it may seem to be an academic exercise to look at the these direct aspects of human behavior, in fact it gives valuable insight into what has previously been a finger-pointing exercise, where human error essentially meant “it was their fault” without looking at the influences that were the behavioral drivers for that individual. It also allows organisations the opportunity to start to examine in detail their own unsafe act reports or accident investigation findings but in a different light. Knowing that a person acted in an unsafe manner is not enough without knowing why and these categories can help with that process. An interesting side note to this is the discussion on plane crashes where ‘pilot error’ was identified as a contributory cause or perhaps even a root cause. The Aviation Safety magazine describes pilot error in two ways; either as an operational error or tactical error. An operational error involves issues with flight training or instruction whilst tactical errors are those made by the behavior of the pilot so even in this highly technical industry, aviation also recognises that human error can be caused by system failings, work environment, human factors and other contributory issues.
Drivers for Human Error Actions
There are multiple types of stressors that can drive human error and it may be a single one or combinations of these that provide the context for an individual: Stressors breakdown into:
- The organisation
- The job
- The individual
Organisational Drivers
If there is one key component to this discussion on organisational influences upon human error, it will invariably be safety culture and management commitment. I used the term ‘one key component’ simply because to me safety culture and management commitment are so closely related, it should be difficult to fit a cigarette paper between the two. An organisation with a positive safety culture will set up its safety management system with a focus on reducing accidents and looking at how improvements can be made.
Individual Drivers
It seems to be stating the obvious that people need to have the required training, skills and knowledge to safety undertake their work but as we have discussed before, an individual is developed within an organisations context. Where higher levels of risk are tolerated in the workplace the safety benefits of all of that training and knowledge will probably be less to the individual. A recent industrial accident in Northumberland, England from back in 2016 illustrates this point where a worker had his leg amputated below the knee when he climbed up onto a woodworking machine to clear a blockage and his leg was caught by the saw blade. In this particular case I think that this fits the definition of a routine violation as this particular saw mill, called A & J Scott had also been fined 4,000 GBP back in 2014 after a worker lost two fingers in another accident with an unguarded log-sawing blade. The cost to this particular saw mill after the most recent court case was a hefty 400,000 GBP fine. 4 The injured person may well have been an extremely competent individual in terms of his woodworking skills, there is no reason to believe that was not the case but the risk environment in which he worked ‘permitted’ him to consider this activity as acceptable. So, it’s not just the competency of workers, their personality fit or their work experience, the risk tolerance level of management is also a key driver for the way in which individuals consider working.
Job Drivers
An organisation will create and be in control of an employees working environment and it is not a great stretch to state that people do not tend to operate well under demanding environmental conditions and where people are placed in situations where they are uncomfortable there is an opportunity for human error situations to occur. Environmental stressors include excessive heat, cold, noise and vibration (we all know how noisy road works outside of our workplaces can really drive you to frustration…), even elements such as poor lighting or poor ergonomic design of workplaces. Additional factors come into play here too such as the workload of the workers, their remuneration (it is difficult working to our individual best capacity when we don’t feel that we are suitable rewarded for our efforts, it is discouraging and demotivating), working with others and whether there are adequate procedures and instructions.
Reducing Human Error
Gaining some understanding into how we behave in the workplace and recognising that these type of human errors can have a potentially damaging impact, what can we do with this knowledge to improve our safety management system?
Developing a safety culture
The biggest barrier to human error behaviors is the development of a safety culture in which the health, safety and wellbeing of employees is considered as a priority and undesirable actions, especially violations are seen as a serious breach of an organisations policies and ethos.
Training
There is an old saying that knowledge is power and providing this type of knowledge to employees and workers can be a very positive start to start a discussion on human error and behaviors. Only an organisation that is interested in effectively managing human error issues would take the time to educate their workforce about them, but this could have a very positive outcome as it shows that there is management commitment to address these issues, that they are important for the organisation to manage and that the working environment can be improved where human error issues are identified and corrected.
Reporting
Every organisation should have a system in place to capture, record and analyse leading indicators, such as unsafe acts and conditions. In light of the types of human error that have been identified, it may be possible for an organisation to examine leading indicator reports in the context of behaviors of workers rather than in the often simplistic way of “he wasn’t wearing his safety glasses so I asked him to put them on” or “she didn’t follow the procedure properly”. The human error dimension adds in the “why” component which could start to identify with a suitable critical mass of these types of reports, what is actually going on within an organisations day to day activities that creates repeated human error deviations to be reported.
Verification
One area that has great value but organisations often do poorly is the verification process of their own systems. Understanding how human errors are manifested gives the opportunity to develop a slightly different approach to a verification process. For example, if we are looking operating procedures we now have the opportunity to ask questions such as:
- Can the procedure be safely carried out in the time frame required and with the people we make available?
- Has the procedure been written by or a contribution made by the people actually undertaking and understanding the task?
- Have all of the people involved have sufficient knowledge to fully implement the procedure and how has that been assessed and verified?
- Where is the evidence that the procedure is being followed as it’s documented?
Recognising that knowledge deficiencies, over-complex or incorrect procedures and other issues that can create mistakes, lapse’s and slips can modify behaviors in a negative way, how do we approach this particular issue? In terms of verification processes, consideration needs to be given to developing a question set to look specifically at these core issues and this may start to eliminate these error types and reveal whether the safety management system is working as effectively as it should be. One interesting aspect of undertaking safety management audits on often quite large organisation is that management sometimes don’t really know what is going on across the entire scope of their system, primarily because they are not sure of the questions to ask about their own system to get the information that management need. This type of approach can give some direction in that regard.
Communications
Safety meetings are an excellent forum for the two-way exchange of information and once a workforce has sufficient knowledge and understanding regarding human error types, workers can be encouraged to identify and report where mistakes, lapses, slips and violations may be occurring.
Summary
People are vulnerable to many kinds of influences on them which impact how they behave at work but it’s important to recognise that many of these influences can be changed or modified. Human error is not about a person making a mistake, it’s about finding out what kind of mistake was made and how did an organisations management system create that opportunity and how can that negative influence be corrected. However, correcting and improving any system can only be successfully achieved within a positive safety culture.
This example is used as it was a real life scenario that occurred after an investigation into the loss of the 1998 Mars Climate Orbiter where the adjustments to its trajectory to Mars was done by the ground computer in imperial units using pounds/seconds whereas the adjustment made on the space craft should have been in newton/seconds. Since there is a 4.5 factor difference between the imperial and metric units, the adjustments actually made grossly underestimated the corrections required and the spacecraft was lost. It is assumed it either crashed into Mars or bounced off of the atmosphere due to the wrong trajectory path it was given during the voyage using the wrong units.
References
2 -https://www.ntsb.gov/news/press-releases/Pages/PR20130129.aspx
3 – HSG48 – Reducing error and influencing behaviour, p17
5 – FATAL ACCIDENT INVESTIGATION REPORT – Isomerization Unit Explosion Final Report – Texas City, Texas, USA, 5.20.1 Operations, p142
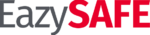
Discover our Safety Training Platform
Train your employees anytime, anywhere with our environmental, health, safety and wellness training platform.
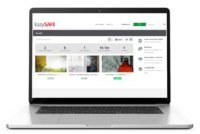
TAILORED TRAINING
Discover our safety training courses and ehs onboardings, which can be customised and offered in several languages.
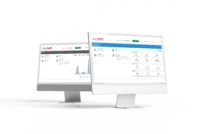
SAFETY MANAGEMENT
Ensure the distribution of your safety policy by training your permanent, temporary or seasonal staff.
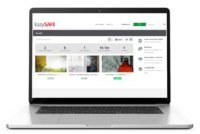
GLOBAL MONITORING
Simplify the management of your safety policy thanks to the numerous dashboards and training reports.