Tailoring Safety Training for your Staff & Contractors
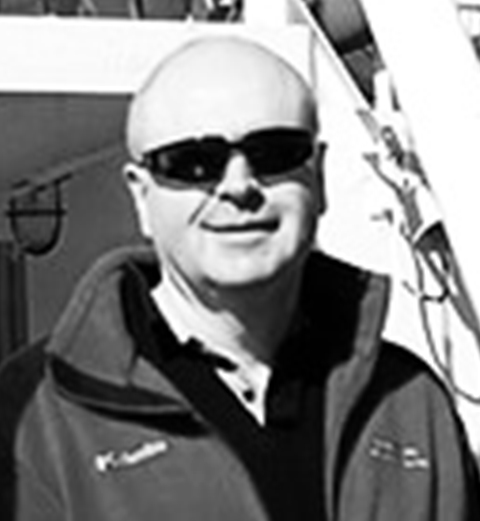
ANDY TILLEARD
EHS Consultant
EazySAFE
This discussion looks at the safety issues that are related to lifting operations, including equipment and accessories and what general arrangements need to be in place to safely manage this type of hazardous work.
Lifting operations cover a surprisingly wide range of workplace activities and equipment, ranging from the use of mobile and fixed cranes, forklift trucks and other similar self-propelled workplace vehicles, lifting platforms on vehicles for people and goods, systems for lifting performers in the entertainment industry and mobile elevated work platforms for lifting and positioning people.
“Not only should lifting equipment be considered in terms of their special lifting capacity, but also as work equipment.”
Rather than focus upon one particular aspect of lifting operations, this discussion will address:
- The minimum elements that need to be in place for lifting equipment as work equipment.
- The issues that need to be managed for safe lifting.
For work equipment overall, which will also include equipment used for lifting operations, the general employer obligations include:
- Regular maintenance and appropriate inspections.
- Instruction and supervision of employees.
- The provision of training and information for its safe operation.
- Safety and hazard signage that is suitable and provides relevant information to users and third parties.
- Suitable control devices, guards and other protective devices to prevent injuries to employees and third parties.
The legal framework
The legal framework for lifting operations and associated equipment is based upon the general requirements of the Safety, Health and Welfare at Work Act, 2005 relating to the provision of safe work equipment. The Safety, Health and Welfare at Work (General Application) Regulations, 2007 as amended deals with lifting operations and lifting equipment within the various clauses covered in Part 1, Chapter 2 – Use of Work Equipment. The clauses are often specific to a different type of lifting equipment; general requirements for all work equipment used for lifting loads, work equipment used for lifting both goods and people, cranes including scotch and guy derrick cranes, hoists and lifts, specific instructions required when people are to be lifted and lifting non-guided loads. A scotch crane, by the way, is an older style of crane design with a mast supported by a back brace with a boom that extends from the base of the mast.
Technical elements
We can think that lifting equipment as the machinery for the lifting of loads and lifting accessories are those items that are between the lifting equipment and the load itself, specifically items such as shackles, chains, harnesses, barrel clamps, spreader bars and other items that attach between the load and the lifting device. In the UK, lifting equipment covers both of these terms under LOLER.
Lifting equipment must be:
- Lifting equipment is appropriate for the task and clearly marked with its safe working load (SWL). The certified testing of lifting equipment is the only time a certified SWL can be is exceeded.
- Lifting equipment used to lift or position people must be designed for that task. The use of forklift trucks and teleporters to lift people off of the ground to work at height are unfortunately not uncommon events on worksites.
- Lifting equipment is examined, tested and certified by a competent person according to requirements.
Organisational elements
Employers need to ensure that organisational issues are in place:
- Do lifting operations come under an organisations permit to work system? This will depend upon how an organisation assesses the hazard of lifting activities. Offshore, lifting operations are often considered as a PTW activity.
- These activities are risk assessed from both a generic perspective for repetitive activities or task-specific for one-off or non-standard lifts.
- Lifting operations are planned. Some organisations have adopted a lifting plan approach to these types of operations. These plans consider all elements of the lift such as pre-use equipment inspections, what barriers are in place, risks from simultaneous operations in the immediate area, PPE requirements, roles and responsibilities for supervising both the lift and the people involved, communications prior to and during the lift (including a toolbox meeting) and how the lift will proceed or indeed stop due to certain circumstances (such as changes in weather).
- All people involved are considered competent for their roles. For example, the lifting equipment or crane operator, riggers and slingers, banksmen and any others who have defined roles and responsibilities must be both trained and have the necessary experience to be competent.
- Lifting registers and records of inspections and testing are maintained so that all parties can have confidence that lifting systems are certified, fit for purpose and in operational condition.
As a part of the risk assessment process, people must be protected from being underneath suspended loads and avoid moving loads over unprotected people. This is especially true where third parties may be present such as the public, site visitors or contractors who may not be aware of the lift or were not involved in the planning phase.
Lifting operations can cover both simple and complex tasks and also utilise a wide range of equipment types and accessories. The approach to take is dependent upon the identified and assessed risks and having adequate controls in place to effectively manage those. Not only should lifting equipment be considered in terms of their special lifting capacity, but also as work equipment to be managed properly outside of their work activity.
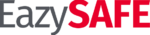
Discover our Safety Training Platform
Train your employees anytime, anywhere with our environmental, health, safety and wellness training platform.
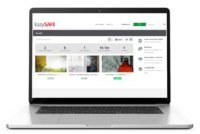
TAILORED TRAINING
Discover our safety training courses and ehs onboardings, which can be customised and offered in several languages.
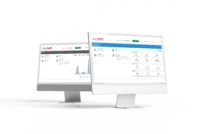
SAFETY MANAGEMENT
Ensure the distribution of your safety policy by training your permanent, temporary or seasonal staff.
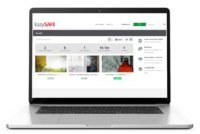
GLOBAL MONITORING
Simplify the management of your safety policy thanks to the numerous dashboards and training reports.