Machinery safety in the workplace
Machinery safety is a critical aspect of workplace safety, particularly in industries where workers operate or interact with heavy machinery. From construction sites to manufacturing plants, ensuring that machinery is used safely and effectively can significantly reduce the risk of accidents, injuries, and fatalities. This article explores the key aspects of machinery safety in Ireland, including risk assessment, methods for preventing machinery-related accidents, and the role of both employers and workers in maintaining a safe workplace.
Machine safety in Ireland
In Ireland, machine safety in the workplace is comprehensively regulated to protect workers from machinery-related hazards. The core legislation, the Safety, Health, and Welfare at Work Act 2005, mandates employers to ensure that machinery is safely installed, maintained, and operated, and that risk assessments are regularly conducted.
Key supporting regulations include:

General Application Regulations 2007 (Chapter 2):
Focuses on safe equipment use, requiring employers to assess risks, select appropriate machinery, and provide user training.

Machinery Directive 2006/42/EC:
Sets EU-wide standards, ensuring machinery sold or used in Ireland meets strict safety criteria. It affects manufacturers, importers, and suppliers, who must guarantee safe equipment design and documentation.

Provision and Use of Work Equipment Regulations (PUWER):
Requires employers to supply machinery that is suitable, properly maintained, and regularly inspected. It includes obligations for preventive maintenance, ensuring that equipment is in safe working order.
The Health and Safety Authority (HSA) enforces these regulations, conducts inspections, and provides employers with safety guidelines. Employers and employees share the responsibility of adhering to these standards, creating a safe and compliant environment for machinery use across sectors.
Machine risk assessment
A machine risk assessment systematically identifies hazards associated with machinery to prevent accidents and injuries by implementing safety controls. This process involves several key steps:
1. Identify Hazards:
The first step is recognizing all potential hazards tied to machinery use. Common risks include moving parts, sharp edges, pinch points, electrical elements, and areas that can cause burns or exposure to harmful chemicals. Even indirect factors, like poor lighting or confined spaces around machinery, may pose hazards.
2. Assess Who May Be at Risk:
Employers must consider not only machine operators but also maintenance staff, nearby employees, or anyone who could be exposed to machinery hazards during their workday.
3. Evaluate the Risk Level:
Each identified hazard should be evaluated by examining both the likelihood of an incident occurring and the potential severity of resulting injuries. Risk levels can be ranked or scored, helping prioritize which hazards require immediate control measures.
4. Implement Control Measures:
Based on the risk assessment, employers must implement effective controls to minimize hazards. These can include physical barriers like guards and emergency shutoffs, safe operating procedures, warning signs, and the establishment of safe zones around machinery. Employers might also introduce job rotations or ergonomic adjustments to prevent repetitive strain and fatigue.
5. Monitor and Review:
Risk assessments should be regularly updated, particularly when new machinery is added, workplace conditions change, or incidents occur. Regular monitoring ensures that control measures remain effective over time.
Preventing machinery risks
Use of Machine Guards
Preventing machinery-related risks involves several key strategies, starting with the use of machine guards, which are the most effective means of safeguarding workers from injuries. Machine guards create physical barriers between operators and hazardous machine parts, significantly reducing the chances of accidental contact. Common types of guards include fixed guards, interlocking guards, and automatic guards, each designed to enhance safety in different operational contexts.
Proper Maintenance and Inspections
Regular maintenance and inspection of machinery are also essential for ensuring safe operation. Equipment should be inspected, cleaned, and serviced according to the manufacturer’s guidelines, with all safety features, such as guards, emergency stop buttons, and alarms, tested regularly to confirm their functionality. Any malfunctioning equipment must be immediately taken out of service and repaired by qualified personnel.
Worker Training
Employees must be trained on safe operating procedures specific to each machine, emergency protocols for shutting down equipment, and the proper steps to take in the event of an accident. Additionally, personal protective equipment (PPE) such as gloves, safety glasses, and hearing protection should be provided to minimize exposure to hazards.
Lockout/Tagout Procedures
Implementing lockout/tagout (LOTO) procedures is crucial to preventing accidental startup or energy release while maintaining or repairing machinery. LOTO ensures that machines are fully de-energized and secured until maintenance is complete, safeguarding workers from unexpected hazards.
Creating a Safe Work Environment
Workspaces around machines should be well-lit and free of obstructions, with clear signage and warnings displayed in areas where machinery is in use. Establishing a safe traffic flow for workers and vehicles around machinery reduces the risk of accidents, fostering a culture of safety in busy work areas.
In Ireland, compliance with machinery safety regulations is not only a legal obligation but also a moral responsibility. By conducting thorough risk assessments, implementing preventative measures and ensuring that workers are properly trained, employers can significantly reduce the risks associated with machinery use. Prioritising machinery safety creates a safer, more productive work environment and helps prevent accidents, injuries, and costly downtime.
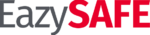
Discover our Safety Training Platform
Train your employees anytime, anywhere with our environmental, health, safety and wellness training platform.
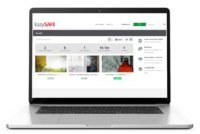
TAILORED TRAINING
Discover our safety training courses and ehs onboardings, which can be customised and offered in several languages.
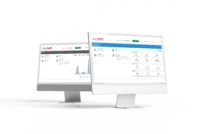
SAFETY MANAGEMENT
Ensure the distribution of your safety policy by training your permanent, temporary or seasonal staff.
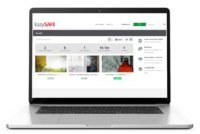
GLOBAL MONITORING
Simplify the management of your safety policy thanks to the numerous dashboards and training reports.