Personal Protective Equipment
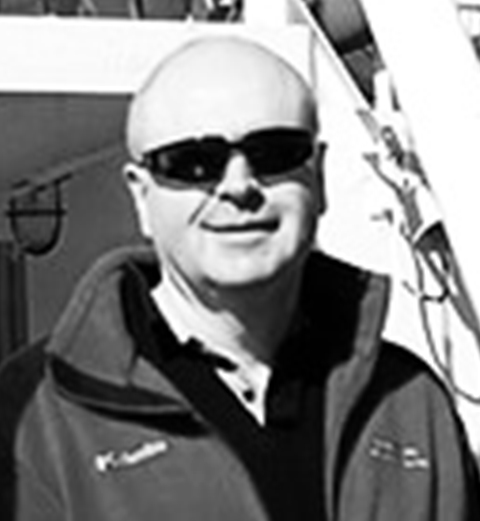
ANDY TILLEARD
EHS Consultant
EazySAFE
Personal protective equipment (PPE) is one of the most useful, but also the most misunderstood risk control measures available in the workplace. The correct PPE can provide very robust barriers to hazards but it must be used in the right context which unfortunately is not always the case in the workplace. What is PPE? PPE is “all equipment designed to be worn or held by an employee for protection against one or more hazards likely to endanger the employee’s safety and health at work, and includes any additions and accessories to the equipment if so designed…”
PPE is used to protect an individual against a workplace hazard and will be designed to protect specific parts of the body or the whole body against a physical, chemical or biological hazard, such as using ear defenders to protect against occupational noise exposure or using a safety harness to protect against a fall from height.
The legal framework
The legal framework for personal protective equipment is based upon the general requirements of the Safety, Health and Welfare at Work Act, 2005 relating to the General Duties of Employers, the General Duties of Employee and Persons in Control of Places of Work (e.g. 13(1)(g)) and the Principles of Prevention.
The Safety, Health and Welfare at Work (General Application) Regulations, 2007 as amended deals with personal protective equipment within the various clauses covered in Part 2 – Workplace and Work Equipment, Chapter 3 – Personal Protective Equipment. Schedule 2 also references personal protective equipment in Parts A and B which deals with types of PPE and the industry sectors in which they are used.
European regulations exist to giving effect to Regulation (EU) 2016/425 of the European Parliament and of the Council of the 9th March 2016 on personal protective equipment. These are known as the European Union (Personal Protective Equipment) Regulations, 2018 in Ireland. This EU regulation ‘…is to ensure common standards for personal protective equipment (PPE) in all Member States in terms of protection of health and the safety of users, while enabling the free movement of PPE within the Union.’ 2
In addition, specific regulations, their associated Code of Practice, safety data sheets for chemicals and industry-specific guides may specify particular PPE requirements depending on the associated risk factors. For example, gloves are referenced in the 2013 Code of Practice for the Safety, Health and Welfare at Work (Biological Agents) Regulations 2013 and high visibility clothing is discussed as a control in the Health and Safety Authority document Safe Quarry – A Guide for Quarry Workers.
Risk assessment
The risk assessment process is critical in the identification, analysis and evaluation of PPE as it is considered to be the control of last resort. This is a fundamental issue that is not always clearly understood by employers, some of whom do not always understand or appreciate the use of the hierarchy of control methodology in the risk assessment process, meaning that other controls to avoid or manage risk must be considered first. Many employers therefore often default to the use of PPE when other more suitable and effective controls are available. However, when PPE is chosen appropriately it has a number of significant benefits as a control:
- It is often cheap to buy, is readily available and is easy to replace when it’s defective.
- PPE is made to high standards which can be identified by the use of the CE mark and from the relevant stated ISO standard.
- Different types of PPE are available to suit personal requirements.
- PPE is available to protect against very specific hazards such as dust, vapours and fumes etc.
- Improvements in material technology often mean more effective PPE over time.
- Improvements in design can mean that PPE can be fashionable to wear for workers.
However, the use of PPE must be considered in the following context:
- The failure or incorrect use of PPE can exposure the wearer directly to the hazard which may result in both acute and chronic occupational injury or illness.
- PPE only protects the individual wearer and is not a collective measure.
- A weak safety culture will almost certainly be a barrier to the effective use of PPE or promote the inappropriate use or non-use of PPE.
- Personal PPE may require regular cleaning, inspection and maintenance and therefore theoretical levels of protection may not be maintained.
- The use of PPE always restricts the wearer to some degree, especially when different but incompatible types of PPE are worn together.
- The effective use of PPE often requires a high level of supervision of PPE users.
- Employees and contractors are not always instructed and informed about the weaknesses or vulnerabilities of using the incorrect PPE or not using PPE as specified.
Employer considerations
Where PPE is to be used, the two most important elements that need to be in place are that of an effective risk assessment process to ensure its appropriate use and a company procedure as to how PPE is going to be holistically managed (from identification of hazards and appropriate PPE, procurement, maintenance, storage, inspection and maintenance and ongoing day to day management). Other considerations also include:
- Employers should provide suitable information and instruction on the correct use of PPE where this is appropriate. Providing training on how to wear safety glasses may not be appropriate, but would be required for specialist breathing gear used for a confined space entry or the correct use of a chemical hazard suit. Once again, the risk assessment process should identify the appropriate mitigations depending on workplace risk.
- Employers must take care that any chosen PPE fits the user and special care is required where medical conditions may be present for PPE users, especially for respiratory protective equipment.
- One type of PPE may not suit all users – examples include providing both ear muffs and ear plugs to protect against workplace noise.
- Employers must pay for the cost of PPE for their employees, although they may charge is the user if self-employed.
- Purchase PPE from a reputable supplier and use a recognised brand name manufacturer – All PPE must be marked with the CE mark as this is a legal requirement under the European Union (Personal Protective Equipment) Regulations, 2018.
Employee considerations
Employees are required to comply with wearing PPE where it has been identified in the risk assessment process as a necessary control and employees should also report defects in PPE to management.
PPE it can be an effective and economic means to protect a user: it is generally designed, readily available and affordable but it does require systems in place for its effective management. On the downside, PPE is often seen as a means to give the illusion of protection against hazards because it is cheap and easily accessible. However, because it is a control of last resort there are many ways in which the incorrect use of PPE or the use of incorrect PPE can expose wearers to many different and potentially dangerous workplace hazards. The provision and use of PPE must be considered in the context of risk and be in compliance with regulations and industry guidance.
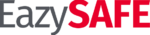
Discover our Safety Training Platform
Train your employees anytime, anywhere with our environmental, health, safety and wellness training platform.
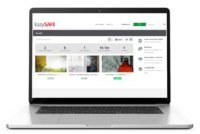
TAILORED TRAINING
Discover our safety training courses and ehs onboardings, which can be customised and offered in several languages.
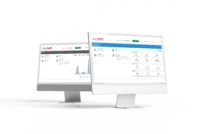
SAFETY MANAGEMENT
Ensure the distribution of your safety policy by training your permanent, temporary or seasonal staff.
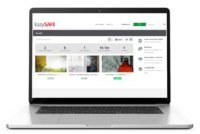
GLOBAL MONITORING
Simplify the management of your safety policy thanks to the numerous dashboards and training reports.