The Push for Zero
ANDY TILLEARD
EHS Consultant
EazySAFE
In recent times there has been the emergence of a new philosophy in safety which has at its heart the concept that all workplace accidents are preventable. To promote this, schemes and programmes have been developed that use the word zero in their title. The word zero is very evocative in safety as it’s an absolute term and there is not too much in how risk is managed to create a safer working environment that is absolute.
It is not just in the realm of occupational health and safety that we are seeing zero used, it also applies to other areas where accidents have a significant impact such as in road safety. Some road safety plans have adopted the zero concept but the use of this term could be misleading so it’s important to understand at the context of its use.
For example, the Government of Western Australia and the Road Safety Commission recently launched a road safety initiative called ‘Towards Zero’ with the admirable aim of significantly reducing the number of road deaths by 2020. The use of the word zero is interesting in this regard as it is widely acknowledged that whilst all accidents may be theoretically preventable, history and real life teach us that accidents still occur. Therefore zero is not actually achievable for road deaths but to their credit the ‘Towards Zero’ programme acknowledges this fact. Their website states that “We recognise that it is probably not possible to avoid all crashes…” and the driver for the programme overall is that “…we do not accept that any human being should die or be seriously injured on our roads and that we do not accept any death or serious injury as inevitable.” So at the same time it set targets to reduce road deaths but states that zero deaths is aspirational rather than realistically achievable. But does the use of terms such as ‘Toward Zero’ set up an unrealistic expectation in the mind of the public that if we are moving toward zero now, logically at some point we must reach it? In OHS in Europe there was an initiative from within the EU to study another safety reduction / prevention programme that was developed to reduce workplace accidents and this scheme has the title ‘Zero Accident Vision’. The concept of “ZAV is the ambition and commitment to create and ensure safe work and prevent all (serious) accidents in order to achieve safety excellence”. This is another example where zero has been used but this programme has also qualified the use of the term with the word ‘serious’ when it talks about preventing all workplace accidents.
The use of the term zero for these schemes has created a significant amount of dialogue in safety circles as it almost implies that zero accidents is doable but even the most optimistic person would be hard pushed to accept that criteria. So what are these schemes actually promoting and is the use of zero misleading? To understand the zero approach, we need to appreciate that its use is conceptual rather than literal and that the context for its use is important. The problem with the word ‘zero’ is that it is unambiguous, zero means exactly what is says so whilst zero serious accidents may be achievable (and I’m not saying that it is in reality) zero accidents will never be. If the stated aim is qualified as zero serious accidents, it would make sense that that is a programme that is worth taking note of. After all, the accidents that we see on the news and read about in the newspapers are generally the serious ones. We know from extensive research and from far too many accident investigation reports that serious workplace accidents are not blue sky events; they happen when organisations don’t heed the warning signs that are present and there are always warning signs. That being the case, these major events are all preventable if an organisation has a focus to effectively manage risk and it is done in a serious way.
The drive for zero also creates a potential paradox; if we get close to zero in improved OHS accident performance, where are the drivers for further improvement and where will the lessons that we need to learn come from? Historically, major workplace accidents have been powerful drivers for making improvements to safety performance including changes to legislation, procedures and standards, improvements in the regulatory environment and in other important areas.
Unfortunately humans are all too predictable and it is certain that there will be future serious workplace accidents and these will generally be from organisations that:
- are committed to good safety performance but their top management actually don’t fully understand what is really going on under the surface, or
- may not be as committed to good safety performance as they think they are and rely on luck and gambling to an extent to avoid serious workplace accidents.
When the accident investigations for these future events are completed, the same usual causative suspects will come to the fore; lack of management commitment, failure of procedures, a lack of communications, reduction in resources, ineffective verification processes and so on. These organisations will not have learnt the lessons from previous workplace accidents elsewhere and will be making the same mistakes as others in the past.
In the future, there will continue to be many organisations who will operate in a reckless fashion, whether schemes like the Zero Accident Vision exist or not. But for those that choose to adopt this approach, one has to be careful that these zero referenced programmes are not seen as some kind of magic bullet. Safety performance will not magically improve just by adopting ZAV. As ever, it is the vital human component at management and worker level that reflects how an organisation actually operates. Nevertheless, any scheme that actively promotes and improves OHS performance or encourages new participants to its potential benefits has to be encouraged and seen as a positive development.
In other areas, the use of zero also has to be carefully considered. There can be a tendency for organisations to use zero as a quick or even lazy way to create corporate or project OHS targets and objectives. Zero fatalities, zero lost time incidents and zero spills to the environment are examples which are really stating the obvious but these don’t show in any way how targets will improve the system performance although they may reflect the desire of a company to prevent workplace accidents. Taking the environmental spill example, if a spill were to occur, even a small one that zero spill target has not been met and so now can we consider that zero target as a failure? Is having one adverse event a failure when an organisation has been successful in preventing many other potential spills through effective risk management? Surely that is a success overall. Of course, no organisation would have an OHS target for the year of ‘less than 5 fatalities’, so in this regard zero would seem to be appropriate but its use must be carefully considered. Let’s look at this from another perspective. Flying is often cited as the safest means of travel but on occasion a news story appears about a plane crash with people being killed. Of course these are terrible events for everyone involved but we all still travel by plane in spite of these tragedies because we accept the generally minimal risk.
Would we actually believe any aircraft manufacturer who made a claim that ‘our planes have new zero crash technology’? The RMS Titanic sinking in 1912 put those ‘this ship is unsinkable’ type claims to bed and we never see them now and today we still consider flying a very successful activity in spite of rare but deadly crashes. In some contexts the use of zero does not make sense or is just plain crazy…
Make sure that zero is used appropriately in measuring the performance of your safety management system, whether it’s in individual leading and lagging indicators, policy statements or targets and objectives. The extent to which any organisation has the capability to actually claim zero as achievable for any OHS metrics depends on many factors such training, proactive HSE reporting, the safety culture, etc. Choosing zero for a target but not achieving it can also mask a lot of good work that is carried out on a daily basis to achieve good OHS performance, with perhaps one failure overshadowing really good work being done. If your safety management system is making continual improvements year on year, that is as good a measure as you can get, but treat zero with caution and understand what it means in your own context.
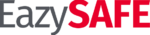
Discover our Safety Training Platform
Train your employees anytime, anywhere with our environmental, health, safety and wellness training platform.
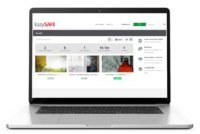
TAILORED TRAINING
Discover our safety training courses and ehs onboardings, which can be customised and offered in several languages.
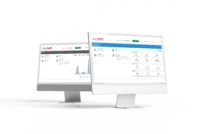
SAFETY MANAGEMENT
Ensure the distribution of your safety policy by training your permanent, temporary or seasonal staff.
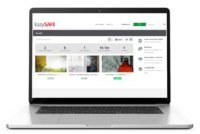
GLOBAL MONITORING
Simplify the management of your safety policy thanks to the numerous dashboards and training reports.