The Importance of Completing Corrective Actions
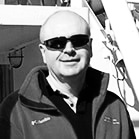
ANDY TILLEARD
EHS Consultant
EazySAFE
Corrective and preventative actions (CAPA’s) are generated as outputs from a wide range of safety management processes such as meetings, inspections, accident investigations, unsafe act and unsafe condition reporting and from audits, and are simply measures that need to be undertaken to ensure that a particular requirement is implemented. The actions are either corrective actions or preventative actions; a corrective action means a situation has been re-instated to its original state, so replacing a broken window is a corrective action. A preventative action will put into place arrangements which will prevent a re-occurrence, to stop the window being broken in the first place. In any event, the particular action type is not so critical but the process by which an action is identified, evaluated and closed out certainly is. “If the entire workforce is on board with pro-active reporting of issues, that means a lot of eyes are looking out for and noticing problems across a lot of processes.”
To understand the importance of effectively managing CAPA’s, we need to appreciate that the primary driver of our management system is that of continual improvement.
Since the only certainty we have is that of change, a safety management system that does not change will soon become outdated and increasingly irrelevant but more of a concern will be the slowly increasing risk profile for the organisation. Rather like the frog sitting in hot water analogy, without constant vigilance an organisation may not even be aware of an increasing risk profile until an accident occurs.
CAPA’s, and the procedures to effectively close out and monitor these, provide the constant small corrections required to guide and improve safety performance. CAPA’s come from a wide range of inputs and therefore they reflect how the organisation operates in reality on a day-to-day basis. This is invaluable as it is collective information. If the entire workforce is on board with pro-active reporting of issues, that means a lot of eyes are looking out for and noticing problems across a lot of processes.
In order to get some degree of control of these, the usual approach is to develop a CAPA depository, usually a database or spreadsheet within which all of the generated actions are recorded and their status is constantly updated. There are a variety of terms used to describe this depository such as an Action Tracking Register, or Action Point List or a Remedial Action Plan. Once a CAPA has been entered into the remedial action plan, hopefully that will initiate a documented process that will result in the CAPA being satisfactorily closed out according to the initial requirement within a defined time scale, whether that is days, weeks or months. CAPA’s and their management can also provide some useful feedback on the performance of the safety management system, including:
- It can measure the extent to which management is willing or able to make corrections to their safety management system.
- How tolerant management are of an under-performing remedial action procedure. For example, what process is in place to ensure that:
- what corrective processes are in place for line managers who do not close out actions assigned to them within the target date, and
- how are deficiencies within the system brought to management’s attention.
- The proportion of overdue actions compared to other categories of actions such as Open, Closed or Rejected can be set as a specific safety target for an organisation as a whole and also for internal departments or business units within an organisation. High levels of overdue actions may indicate ongoing issues, for example with a lack of resources such as limited finances, inadequate staffing levels or a lack of management commitment.
In order for there to be a positive result from this information gathering process, CAPA’s have to be actually closed out. Whilst this may seem to be stating the obvious, there are many examples in the real world where corrective actions and/or preventative actions were identified and made available to management but were then ignored. Generating CAPA’s and recording them in a plan is one thing, closing them out to a satisfactory standard, verifying that that has been done and monitoring ongoing compliance is another. If verification processes are not in place there is no guarantee that:
- The action has been closed in the manner that the CAPA originally specified.
- The action has been closed out at all.
- An action which has been closed out does not mean that the same issue cannot deteriorate again into an unsatisfactory state.
Consider this scenario – safety management audits across a range of activities and processes were a regular occurrence at the Texas City refinery site but over time, the follow up on audit corrective actions had been allowed to become less than robust. Findings after the explosion at the site in 2005 found that “There did not appear to be an effective system in place to verify that recommendations from audits were satisfactorily resolved.” “Action items did not appear to be tracked and effectively closed, especially those of nonspecific and cultural aspects.” . Texas City was a totally avoidable accident that killed 15 people and injured close to 200 others. It is to some extent a notorious accident in that so much of what went wrong at the plant on that day was an accumulation of already known issues that had not been corrected and therefore just happened to coalesce at 1:20pm on the 23rd, March 2005. One element of that was of incomplete procedures and practices to track the closure of CAPA’s. Unfortunately, Texas City was not the only devastating accident in recent times where accident investigators identified CAPA’s mismanagement as a contributory factor in an accident.
Lac-Mégantic, the day of the derailment
Can you imagine a freight train, pulling 63 tank cars loaded with crude oil running out of control down a hill into a town and derailing? That was the apocalyptic scenario that unfolded at the sleepy Canadian town of Lac-Mégantic in Quebec in March, 2006.
Fires and explosions from 6,000 cubic metres of spilled crude oil killed 47 people, destroyed 40 buildings and 53 vehicles and caused severe environmental contamination.
Once again, although there was a CAPA system in place, there was no procedure to make sure that CAPA’s were implemented and once again, it was left to the accident investigators to explain what went wrong. “The limited number and scope of safety management system audits that were conducted by Transport Canada Quebec Region, and the absence of a follow-up procedure to ensure Montreal, Maine & Atlantic Railway’s corrective action plans had been implemented, contributed to the systemic weaknesses in Montreal, Maine & Atlantic Railway’s safety management system remaining unaddressed.” That’s a key point in our discussion; it was not the only factor that contributed to the accident, just one amongst many others but a lack of proper procedure introduced an unnecessary and unwanted variable into the railway operator’s safety management system, and of course a variable that would have been so easy to correct.
If you have a CAPA system and have implemented a plan to manage them but don’t follow up on them, it is almost certain that there are stresses in your safety management system somewhere that you do not know about. For mindful managers, that is not a good position to be in and that’s why completing and verifying CAPA’s is an important process.
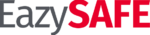
Discover our Safety Training Platform
Train your employees anytime, anywhere with our environmental, health, safety and wellness training platform.
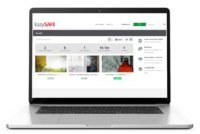
TAILORED TRAINING
Discover our safety training courses and ehs onboardings, which can be customised and offered in several languages.
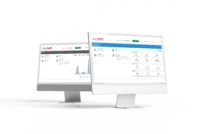
SAFETY MANAGEMENT
Ensure the distribution of your safety policy by training your permanent, temporary or seasonal staff.
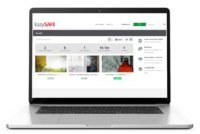
GLOBAL MONITORING
Simplify the management of your safety policy thanks to the numerous dashboards and training reports.